As a member on the fluids subteam during the 2022-23 rocketry season, I executed the design and manufacturing of two end caps for our nitrous oxide tank. These components were incredibly complex and our constraints demanded they fulfill several roles.
- Contain at least 1200 PSI of pressure for a factor of safety of 1.5
- Interface with both the combustion chamber (bottom) and payload (top) through a bulkhead interface. Since the bulkheads need to withstand the rapid acceleration the rocket endures (up to 3000N) it was an incredibly important part of the design.
- Interface with the airframe to ensure it’s adequately retained for flight.
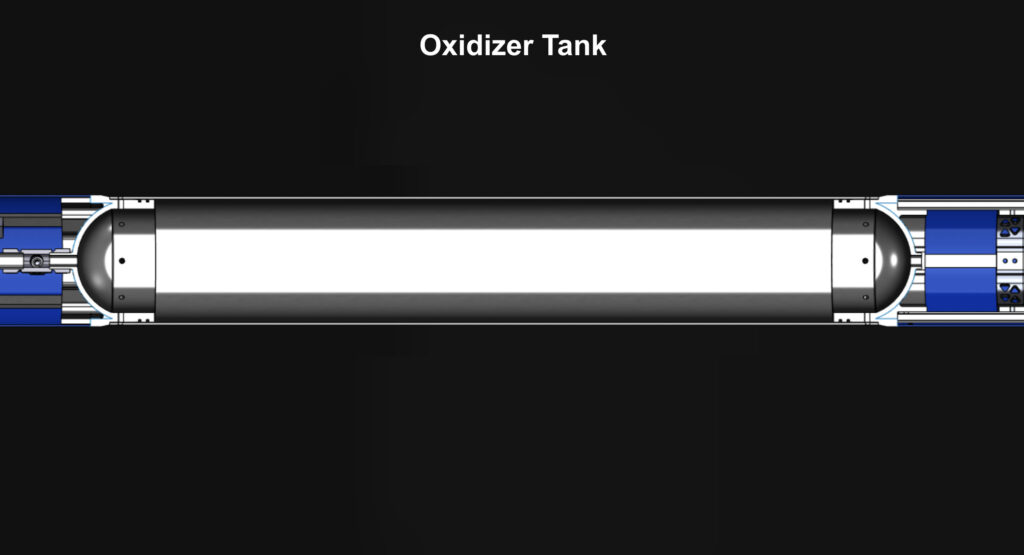
Because of the COVID-19 pandemic, the Columbia Space Initiative Rocketry team members who manufactured the oxidizer tank for the 2021-2022 rocket, which was 4.5″ in diameter, had already graduated. Thus, we were essentially starting from scratch.
The first iteration of the end caps was manufactured over a 4-week period on a Haas ST-20Y and Haas 3-axis mill after using Fusion 360 to CAM it.
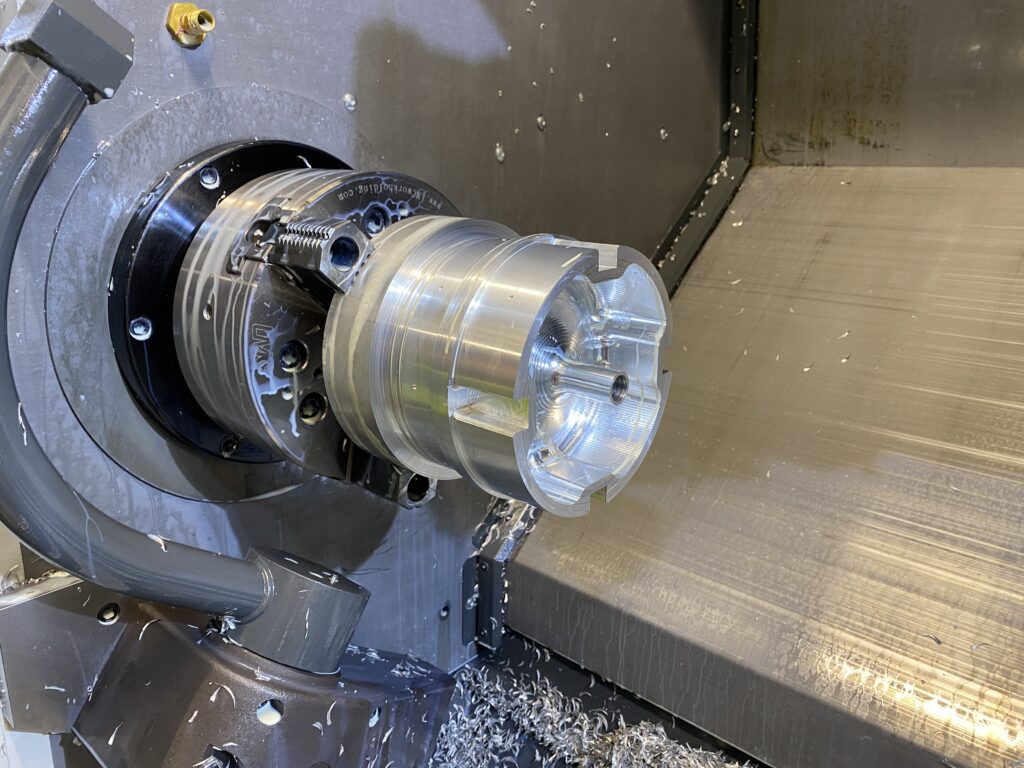
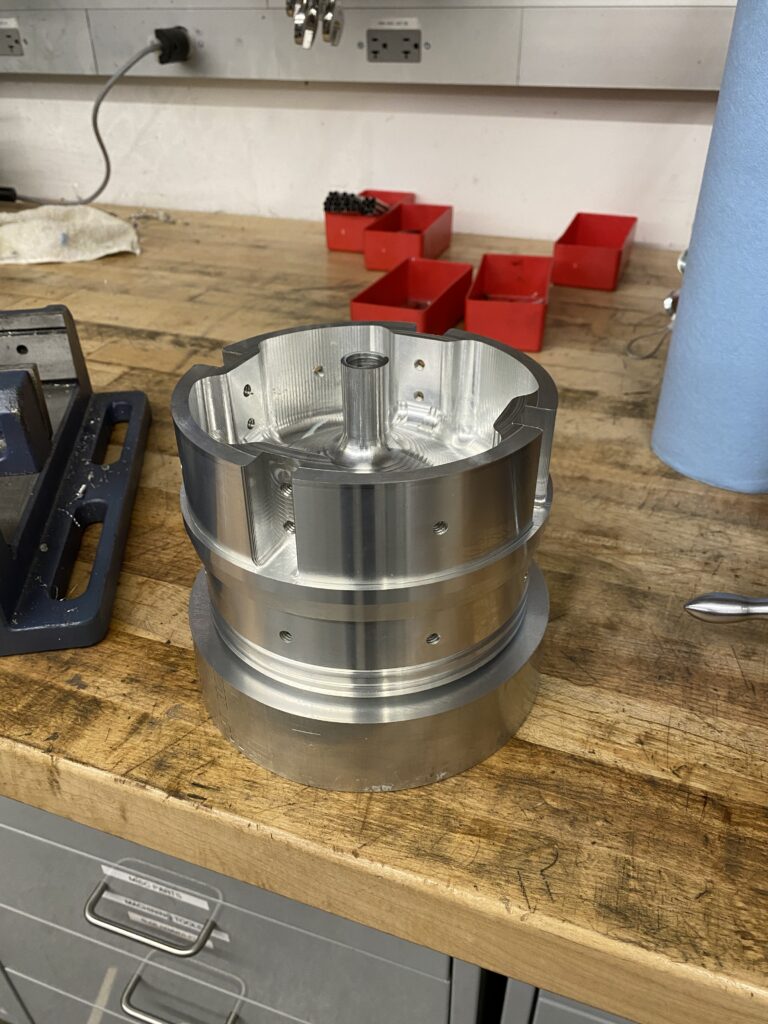
After manufacturing concluded, my team and I began our hydrostatic testing regime. This involved filling the tank completely with water, then using a water pump to test our assembly up to the required PSI.
Unfortunately, hydrostatic testing was a complete failure. Our oxidizer tank failed at 600 PSI, less than the 750 PSI needed for a nominal launch and nowhere near the factor of safety needed to pressurize with a compressible gas (1.5x).

After returning from the failed test, the team and I began to investigate the source of the failure. The first was bearing stress, which is a force induced by the head of the bolts on the outer ox tank tube. We had no knowledge of bearing stress as a constraint, and this served as a learning moment for how to improve pressure vessel design. For the 23-24 school year, I revisited the design from a first principles approach to optimize for mass.
This incident also emphasized the importance of two programatic principles I’ve since taken to heart:
- Test early and often: Hydrostatic testing safely exposed a critical design flaw that would’ve otherwise served as an even bigger program setback.
- Build in schedule margin: Projects rarely go to plan, building in schedule margin helps prevent project setbacks from becoming program blockers.
With the failed test occurring in early April 2023, we worked to achieve a late April static fire goal. Within a week, a fellow fluids subteam member and I remanufactured both end caps with updated parameters. The improvements are as follows:
- Increased holes from 8 to 16.
- Increased hole depth from 0.25″ to 0.43″
- Increased ox tank thickness from 0.125″ to 0.1875″
- Increased airframe holes from 4 to 8
We verified these new parameters by calculating the new bearing stress, which was sufficient such that we had a factor of safety of 2.2 (roughly 1700 PSI). After I finalized both the top and bottom-end cap CAD, we started manufacturing again. Due to the increased hole depth and a lack of 6.5″ stock, the entire part required brand-new CAD and CAM.
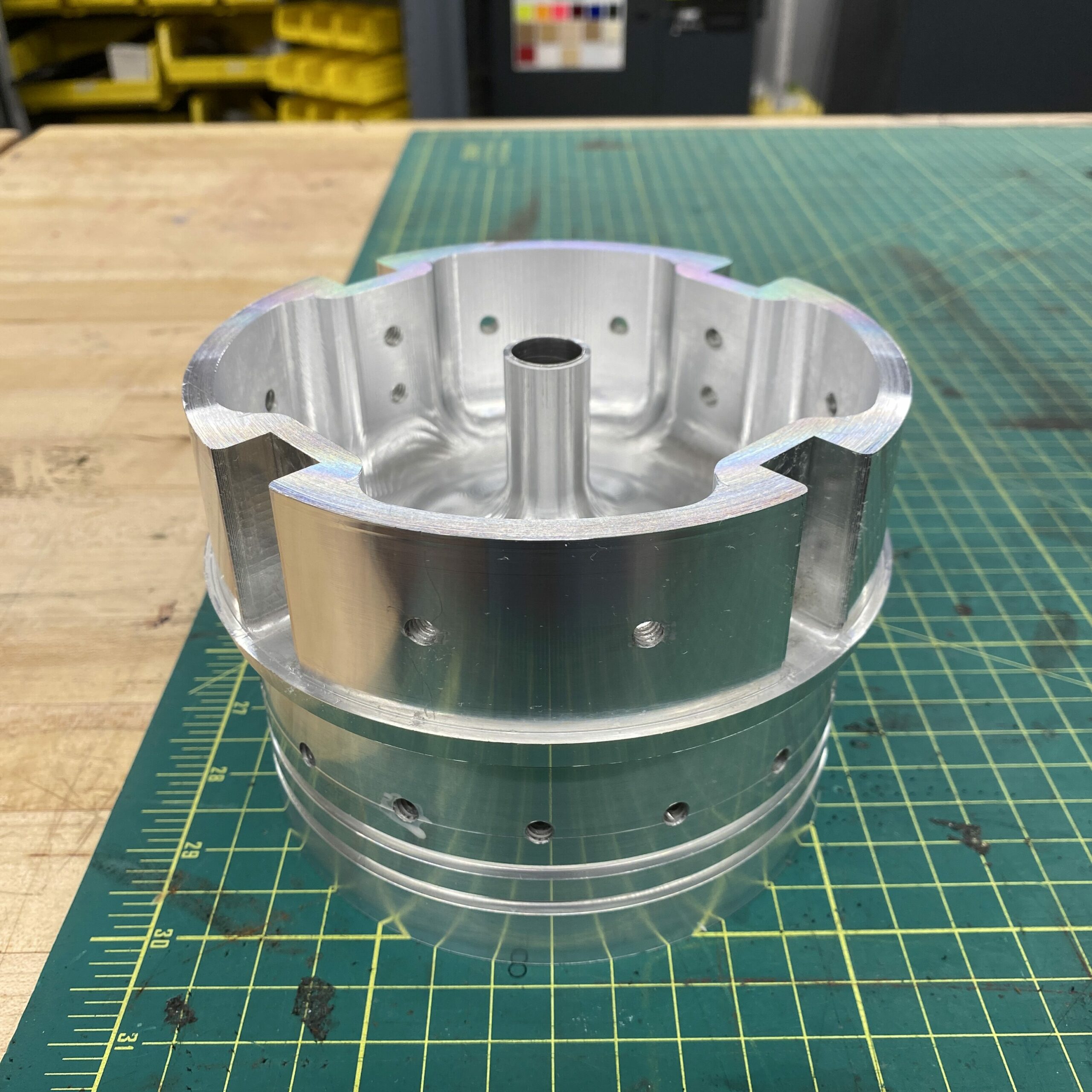
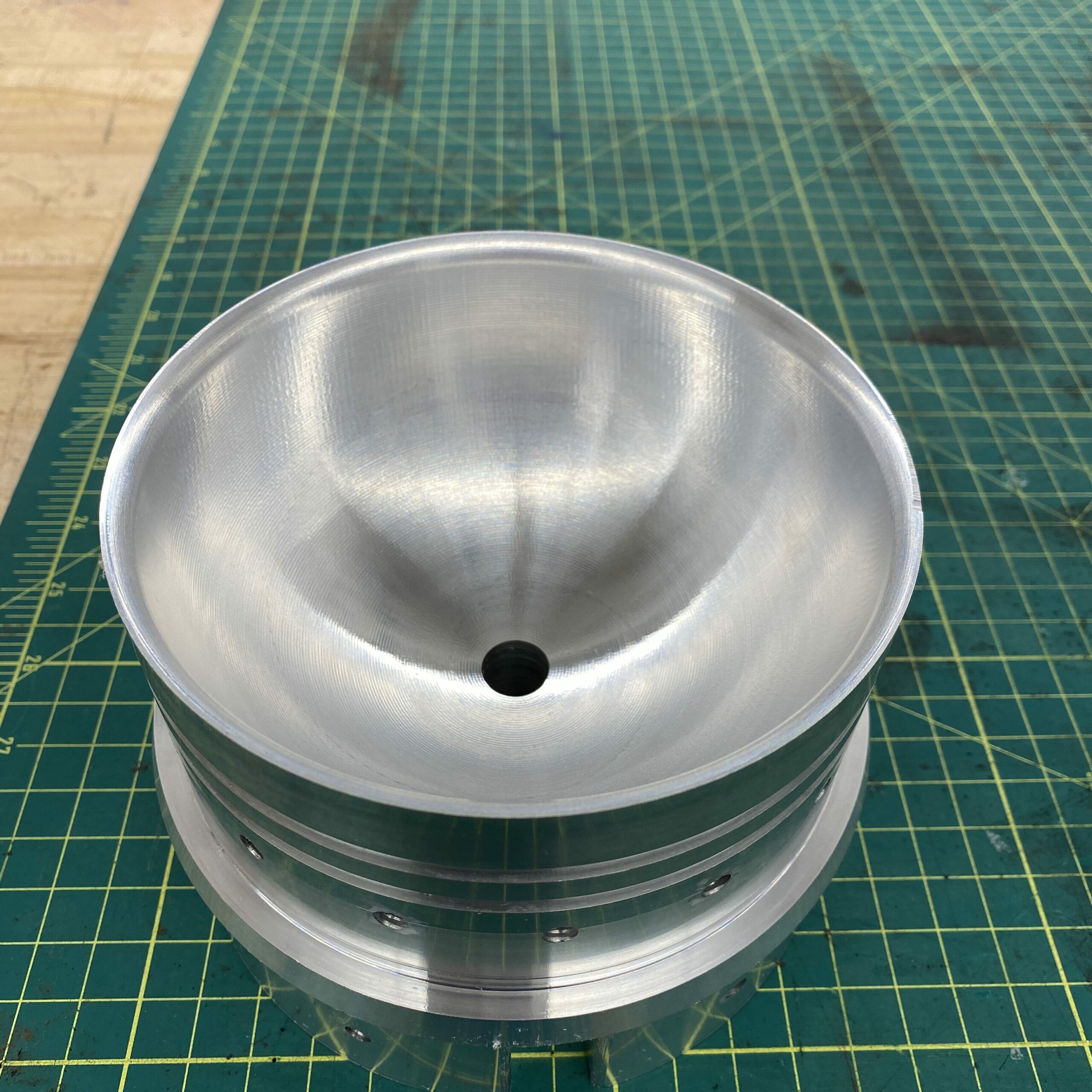
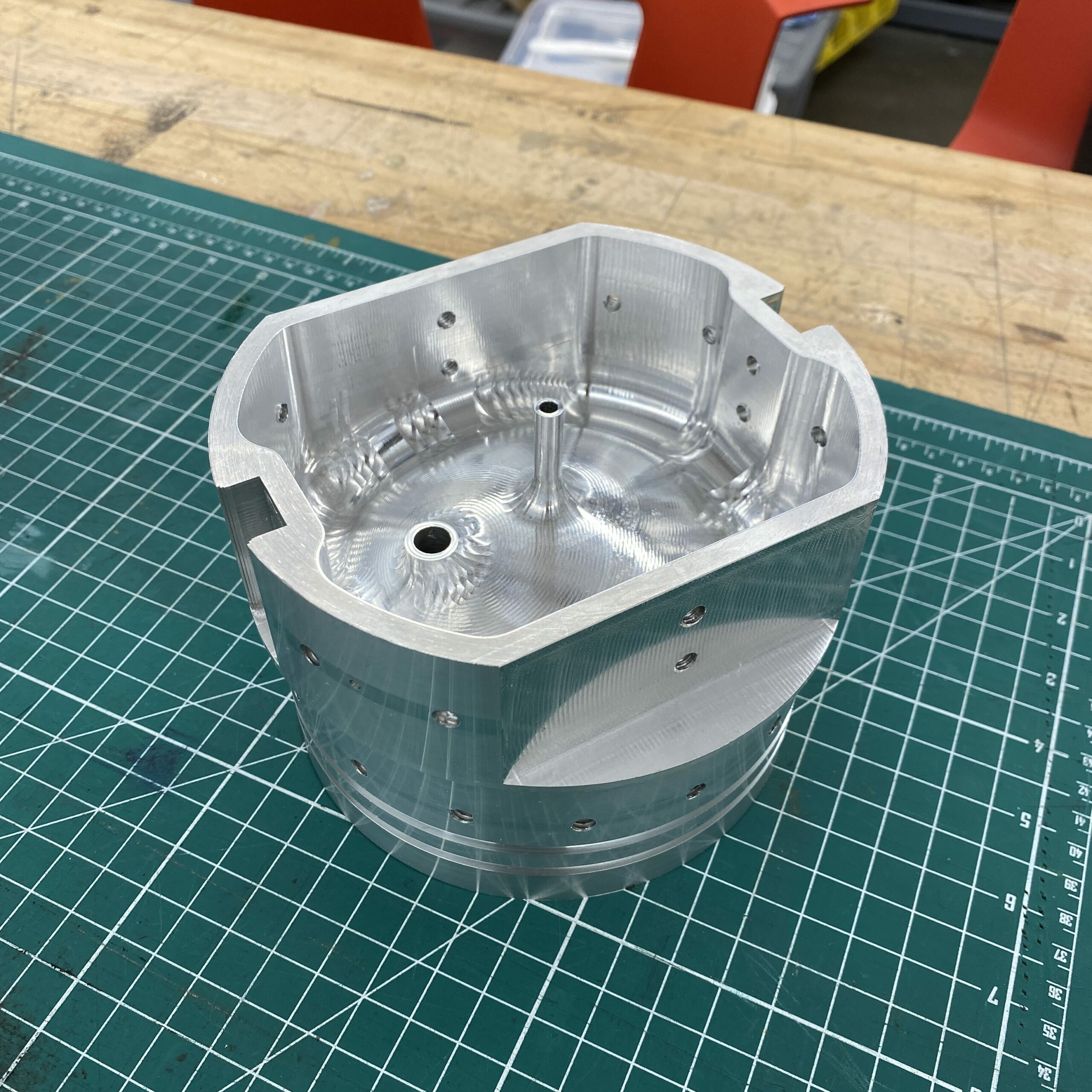
The new end caps were designed and manufactured within a week. Additionally, the quality of machining improved with experience (although reviewing this article 1.5 years later I cringe).
The next challenge was drilling precise 0.25″ holes in our ox tank. Due to error propagation with measuring calipers, it was nearly impossible to manually drill 16 holes as we did with 8 holes. Instead, we stretched the abilities of our lathe to use it as a rotary index.
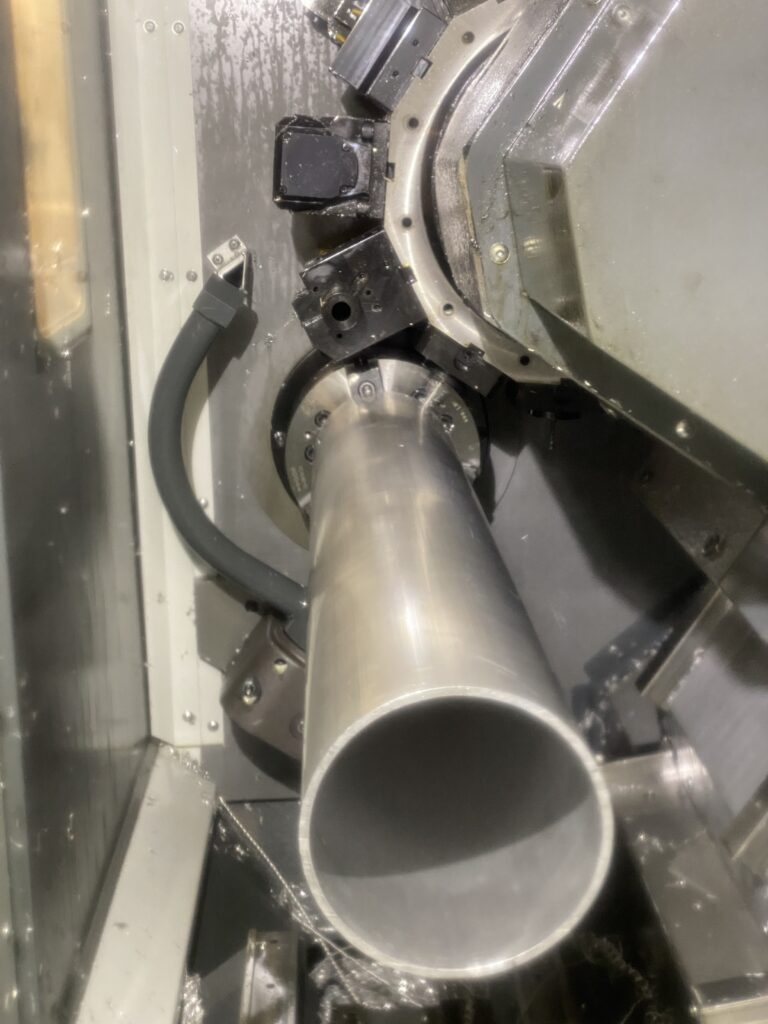
The result was precise holes that aligned perfectly with those on the end caps.
A second hydrostatic test was successful, and the ox tank was validated to 1200 PSI, 1.5x the MEOP of 800 psi. The next step was a cold flow, where we attempt to fill the oxidizer tank with nitrous oxide. We had two successful cold flows, one of which I recorded below. It performed below specification due to an undersized run valve. I concurrently developed a servo-actuated ball valve which remedied this issue, you can read about it here.
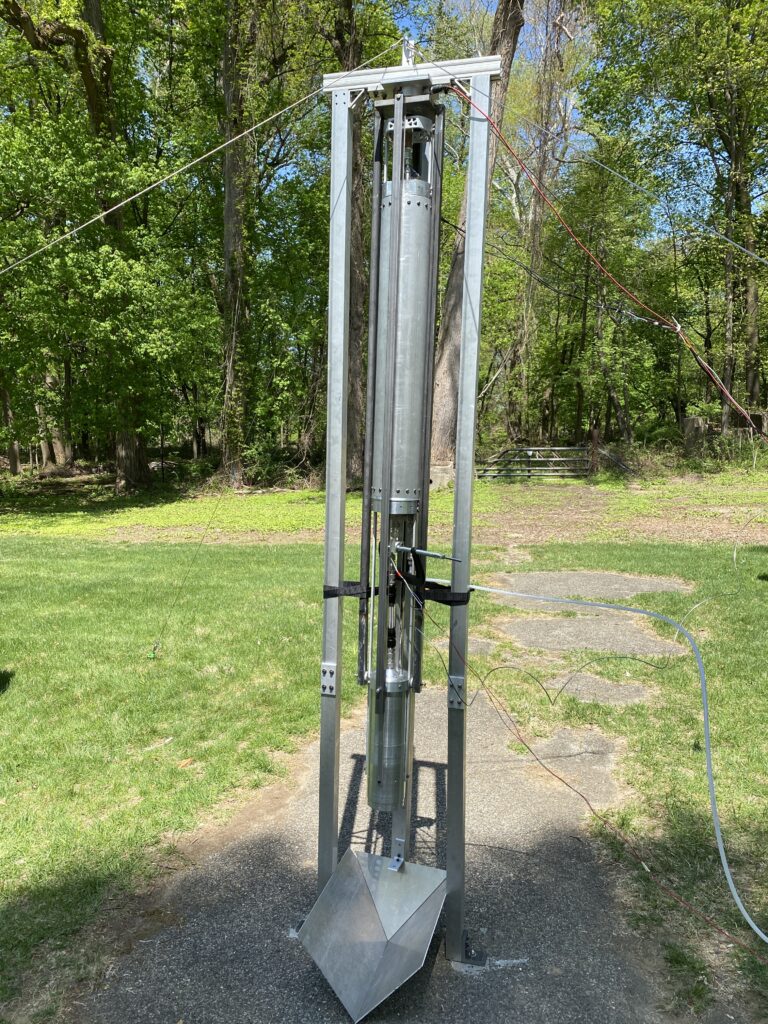
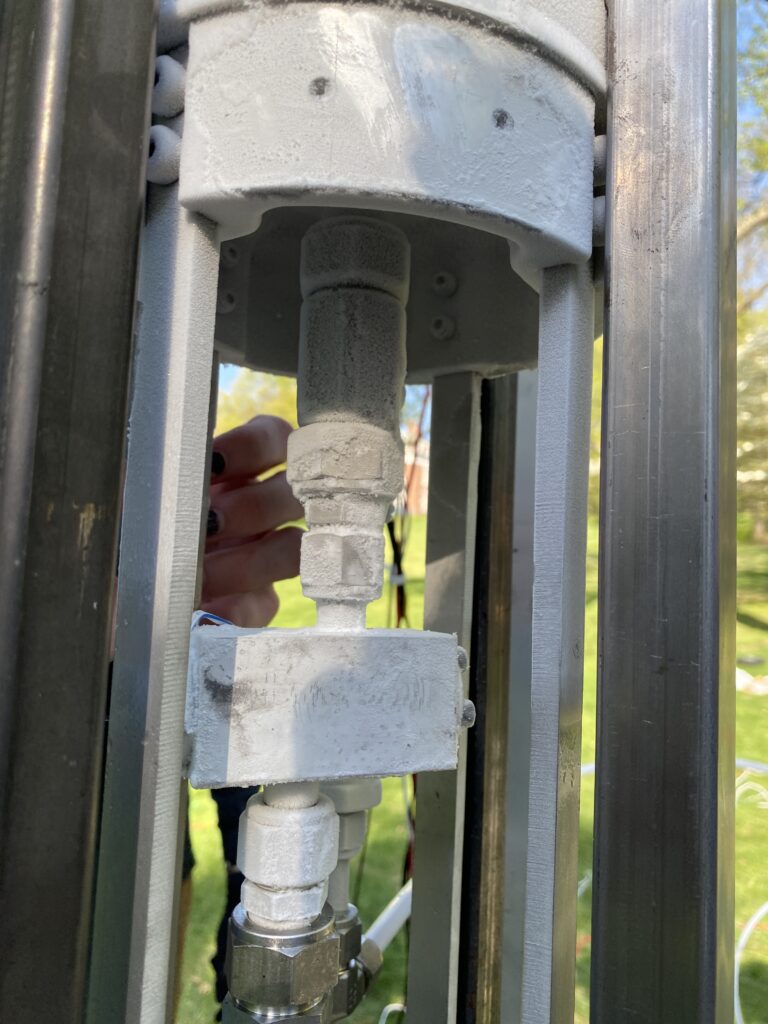
The 2023 oxidizer tank was further validated in cold flows and static fires, and launched in June 2023 on PleaseGoUp. We also successfully recovered the tank, which sustained some damage from the ballistic reentry!
PleaseGoUp Launch, June 2023 at the Spaceport America Cup:
